Breakthrough!!!! To the open waters and beyond!
Welcome to the latest (May 2021) Congleton Hydro Newsletter. After the euphoria of getting Archie successfully installed into his new home, it has been back to the grind, focussing on the completion of the site infrastructure.
A key task has been the welding of the joints in the 1.5metre diameter Weholite inlet pipe. You may recall from previous newsletters that the pipe (made from HDPE – High-Density Polyethylene) is approx. 40metres long and was installed in lengths of approx. 5metres. To maximise waterflow into the forebay tank and hence down Archie’s gullet!! the pipe must be as watertight as possible.
This has entailed welding the joints from inside the pipe. A team of two specialists took about 5 days to complete the task. They used a special “welding gun” which is essentially a “big boys’” soldering iron fed with 5mm diameter HDPE tube via a “hairdryer” pre-heater. As you can imagine, not an easy or nice job—constricted space, trickling water, and fumes from the heated HDPE—well done to the two specialists who worked with a smile!!
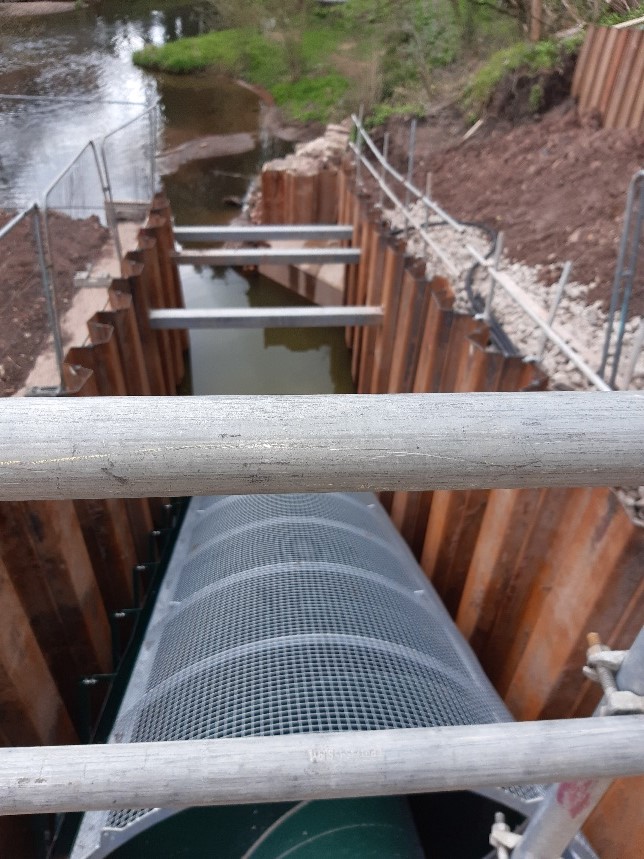

As you have seen from the opening photograph, the piles separating the screw channel and the river were removed. Still no water for Archie though as the inlet piling structure separating the inlet pipe entrance and the river were still in place. Once these piles are removed the only barrier between the river and the hydro system itself is the Inlet Sluice Gate. This is a substantial structure and when in the closed position will turn off the water supply to Archie. This is essential for future maintenance of the system to be carried out safely. The gate is controlled by a hydraulic lift pump, fed from a 3-phase 400 Volt supply from the powerhouse.
In front of the inlet gate is the Trash Screen, too (hopefully catch most of the debris -trees, branches, and whatever else floats down the river—more about this later)
With the gate tested for the correct rise and fall and firmly locked in the closed position (never will be 100% watertight, given the pressure of the river and will always allow a very small trickle through), the time had come for the second but perhaps most important breakthrough—the removal of the inlet piles. Given that the piles are almost 5 metres long and were bashed into the riverbed some months ago, no easy task for mere mortals but short work for a digger, fitted with pull chains and manipulated by an experienced operator.
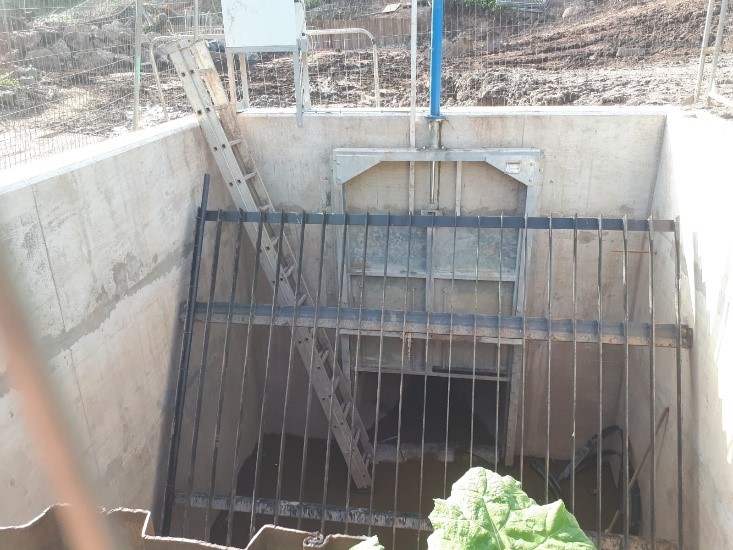
Inlet Sluice gate (in open position) Blue Pipe contains the Hydraulic Ram.

Chain hooked into hole in top of pile, upward jerking from the digger arm and up they come—about 10minutes per pile.
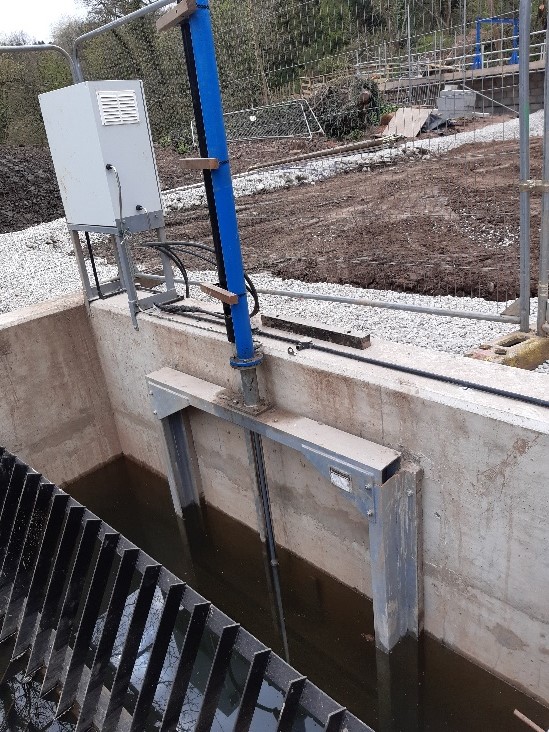
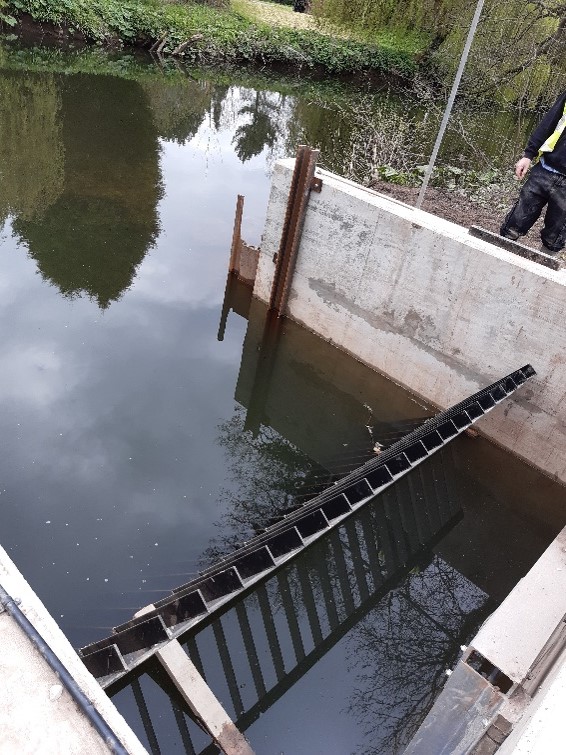
Ready to feed Archie…when the Sluice Gate is opened!!
The channel secured to the wall close to the river is (together with its compatriot on the opposite wall) for use in fitting stop logs (like those used to isolate canal locks) if maintenance work ever needs performing on the sluice gate. Safety railing now needs to be fitted to this inlet structure —to help provide safe working for the cleaning of debris from the trash screen. As well as a barrier fitted on top of the walls, a gridded walkway and safety rail will be fitted between the sluice gate and the trash screen. This will enable an “easier” rake out of debris. Method statements detailing safe working practices e.g., wearing tethered life preservers are being prepared. (Photos of these safety features in a future newsletter).
The eagle eyed amongst you will notice a black conduit running along the top of the wall. This contains the cable for the inlet water level sensor which is located about 500mm off the bottom of the inlet channel. This level sensor is essential for us to ensure we maintain the Environment Agency specified “cosmetic” flow of water over the Weir (during low flow levels—maybe in a very dry summer, we will need to reduce the flow into the system). An additional sensor is installed in the forebay tank and is used to sense any significant difference between the water level at the weir head and the inlet to Archie. The cause for this may be a blocked trash screen and the need for the heavy gang to be mustered to rake it all out. The operation of these sensors was described in the March Technical article (control and monitoring) but as a brief reminder the sensor works on the principle of differential pressure measurement. The sensing element is a taut metal diaphragm between two metal surfaces—essentially performing the function of a complementary pair of capacitors. Pressure differences result in changes in the relative capacitor values and once converted into a suitable signal is used by the control and monitoring system.
As you will have noticed over the duration of the project not everything goes to plan—the weather, Georgian stone piles and so on. But what could go wrong with installing the 40metre long cables from the powerhouse area to the inlet channel—wires for the hydraulic pump and the level sensors and a few spare. The ducting including a drawcord to carry these cables had already been laid. It would only be a matter of 30mins or so to pull these cables through (admittedly quite large steel wire armoured, thick cables). Unfortunately, we had forgotten the knowledge gained in our formative years in the Boy Scouts on how to tie secure knots. All was going well, until with only a few metres of cable left to pull, the “secure knot” parted, and the draw cord end appeared but with no cables attached! Oh dear—hours later but now with a team of four of us, instead of the planned two, we got the cables through. Learning experience –use larger diameter ducting and revisit “how to make secure knots”!!
With all the core site construction work complete, the Civil Contractor – CT Construction, has with a wave of their digger arms, left site and moved onto pastures anew. They have done a great job under very demanding conditions. Hopefully, we can solicit a team photo for the next newsletter.
Now as soon as the Powerhouse is finished, we can install the gearbox, generator and control cabinet and get Archie sparking away. What can be simpler than throwing up some blockwork and a roof——well, some bricklayers and scaffolders would be useful! Wherever you live, I guess there are rucks of new houses in the process of being built, Four Thousand Five Hundred in Congleton alone. This together with the plethora of house modifications, extensions etc. generated by the lockdown has sucked in all the available bricklayers and scaffolders. Finally, after some weeks of searching, pleading, and praying, CT managed to secure a team of brickies from Worsley (North Manchester) to be a on site for a few hours after 4pm. They duly built up the first few courses but then scaffold was needed. Again, after much pleading and praying, scaffolders arrived from Chapel-en-le-frith. The brickies were then persuaded to come back and once on site made rapid progress until the point where the next level of scaffold is needed. At the time of writing (May 2nd), the powerhouse is just four blocks short of the top, fingers crossed scaffolders will be back this week—followed again by the brickies. Then again, fingers crossed, roof will go on in just a few days.
Once the building blockwork is complete, it will be covered in treated wood cladding. This will be installed by ourselves.
The Blue “A Frame” in the powerhouse photographs below, will be used in conjunction with a suitable hoist etc to install the gearbox and generator onto the pedestal. This work with be carried out by RMS (Rotating Machinery Services) from Stoke-on-Trent. Their team has already been on site to assess and determine the suitable method. It is anticipated that together with the install of the Control Cabinet, the work will take two days.
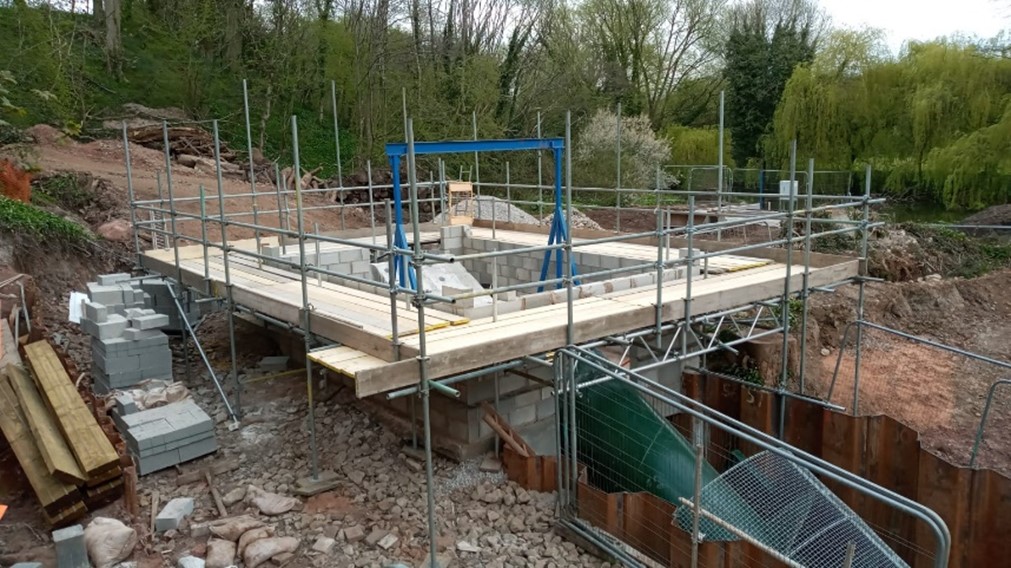
Powerhouse under construction.

The outstanding materials (extra – long recycled composite plastic posts and wooden beams) have been delivered and the final stage of the boardwalk—from the woodland to the Powerhouse is underway and will be completed in the next few weeks. This means that the final length of “export cable” can be laid under the boardwalk from Havannah Lane to the Powerhouse.

The Boardwalk – Entrance from Havannah Lane – The Transition to the Powerhouse
Bottom line is that we have made really good progress this month. Once the powerhouse is complete (cladding is not on a critical path, although will be useful to do it whilst scaffolding is still in place), the raised floor can be installed (approx. 600mm above forebay level to ensure control cabinet is above “once in a 100 year flood level). Gearbox, Generator and Control cabinet can be delivered to site and installed. Once internal Powerhouse cabling has been completed and export cable connected and tested, initial commissioning can commence. Hopefully, this will start in the next couple of months.
Other non-critical path activities also need to be progressed e.g., Boardwalk entrance decking completion, gateway access, distribution, and levelling of the mounds of excess soil on site, woodland management and landscaping and so on.
Although there is no “technical article attachment” this month (Update article on Education programme next month), we hope you have found this newsletter to be informative and of interest. It is intended to give you a picture of how the scheme is progressing and now coming close to fruition. We would welcome your feedback and suggestions for any topics you might like to see in future issues. Please drop us a line at info@congletonhydro.co.uk
As always: Please Stay Alert, Take Care and Stay safe.
Recent Comments